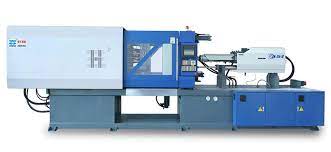
In the realm of manufacturing, precision and efficiency are paramount, especially in industries producing essential components like LED bulbs. One of the crucial machines in this process is the LED bulb injection blow molding machine. This article delves into what these machines are, how they function, their importance in LED bulb production, and the technologies involved.
What is an LED Bulb Injection Blow Molding Machine?
An LED bulb injection blow molding machine is a specialized piece of equipment designed for the manufacturing of LED bulbs. It integrates several processes crucial to creating the outer casing or housing of LED bulbs through a method known as injection blow molding. This process allows for the production of precise, seamless, and high-quality casings that are essential for the durability and performance of LED lighting products.
How Does It Work?
Injection Molding Phase
The process begins with injection molding, where raw materials such as plastic resins are melted and injected into a mold cavity. This mold is specially designed to create the desired shape of the LED bulb casing. The injection phase ensures that the molten material fills the mold completely, resulting in uniformity and consistency in the final product’s dimensions and structure.
Blow Molding Phase
Once the injection molding is complete, the mold containing the molten material (now in the shape of the LED bulb casing) is transferred to the blow molding station. Here, pressurized air is introduced into the mold cavity, causing the molten material to expand and conform to the contours of the mold. This step is crucial for achieving the precise shape and thickness of the LED bulb casing.
Importance in LED Bulb Production
Precision and Consistency
LED bulbs require casings that are not only aesthetically pleasing but also functionally robust. The injection blow molding machine ensures that each casing produced meets stringent quality standards in terms of dimensions, surface finish, and material strength. This consistency is vital for the reliable performance and longevity of LED bulbs.
Efficiency and Cost-Effectiveness
By integrating both injection molding and blow molding processes into a single machine, manufacturers benefit from increased efficiency and reduced production costs. These machines are capable of high-speed production with minimal material wastage, making them economically viable for large-scale LED bulb manufacturing.
Design Flexibility
LED bulb designs can vary significantly based on application and market preferences. The versatility of injection blow molding machines allows manufacturers to experiment with different shapes, sizes, and configurations of LED bulb casings without compromising on production efficiency or quality.
Technological Advancements
Automation and Robotics
Modern LED bulb injection blow molding machines often incorporate advanced automation and robotics systems. These systems streamline the manufacturing process by reducing human intervention, improving cycle times, and enhancing overall precision. Automated systems also contribute to a safer working environment by minimizing the risk of accidents associated with manual handling of molds and components.
Material Innovation
The materials used in LED bulb casings have evolved significantly over the years. Injection blow molding machines are now capable of processing a wide range of plastic resins and additives that offer enhanced properties such as heat resistance, UV stability, and impact strength. These advancements ensure that LED bulbs can withstand diverse environmental conditions and operational stresses.
Energy Efficiency
In line with the sustainability goals of many manufacturers, modern injection blow molding machines for LED bulbs are designed to be energy-efficient. They incorporate features such as servo-driven hydraulic systems, energy recovery mechanisms, and optimized heating and cooling cycles. These measures not only reduce energy consumption but also contribute to lower operational costs and a smaller carbon footprint.
Challenges and Innovations
Complexity of Design
As LED bulb designs become more intricate to meet diverse consumer demands, injection blow molding machines must adapt to handle complex molds and geometries. Innovations in mold design software and 3D printing technology are enabling manufacturers to create molds with intricate details and fine textures, enhancing the aesthetic appeal of LED bulb casings.
Quality Control
Maintaining consistent quality across large-scale production runs remains a challenge for manufacturers using injection blow molding machines. Innovations in real-time monitoring systems, automated inspection technologies, and machine learning algorithms are helping to mitigate these challenges by identifying defects early in the production process and optimizing machine settings for improved product consistency.
Future Trends
Integration of Industry 4.0 Technologies
The future of LED bulb injection blow molding machines lies in the integration of Industry 4.0 technologies. This includes the adoption of IoT (Internet of Things) connectivity, big data analytics, and predictive maintenance capabilities. These advancements will enable manufacturers to achieve greater operational efficiency, minimize downtime, and respond quickly to changing market demands.
Advancements in Sustainable Manufacturing
Environmental sustainability will continue to drive innovation in injection blow molding technology. Manufacturers are exploring biodegradable and recyclable materials for LED bulb casings, as well as implementing closed-loop recycling systems within their production facilities. These initiatives aim to reduce waste generation and promote a circular economy approach to manufacturing.
Conclusion
The LED bulb injection blow molding machine represents a cornerstone of modern manufacturing processes, particularly in the lighting industry. By combining precision, efficiency, and versatility, these machines play a crucial role in producing high-quality LED bulb casings that meet the demands of today’s market. As technology continues to advance, these machines will evolve to meet new challenges and opportunities, driving innovation and sustainability in LED bulb production.